Unlocking the Power of Welding WPS: Strategies for Performance and Security in Manufacture
In the world of manufacture, Welding Treatment Specs (WPS) stand as the backbone of welding operations, dictating the necessary actions for attaining both performance and security in the construction process. Understanding the details of WPS is extremely important to using its complete capacity, yet many companies battle to open real power that lies within these records (welding WPS). By diving into the strategies that maximize welding WPS, a globe of improved productivity and enhanced security awaits those happy to discover the nuances of this important facet of fabrication

Value of Welding WPS
The relevance of Welding Treatment Specs (WPS) in the manufacture sector can not be overemphasized. WPS function as an essential roadmap that details the necessary actions to guarantee welds are performed constantly and correctly. By specifying vital parameters such as welding procedures, materials, joint layouts, preheat temperatures, interpass temperature levels, filler metals, and post-weld warmth treatment needs, WPS offer a standardized technique to welding that enhances performance, high quality, and safety in construction processes.
Adherence to WPS assists in attaining uniformity in weld top quality, decreasing the chance of problems or architectural failures. This standardization likewise facilitates compliance with sector regulations and codes, making sure that fabricated structures fulfill the required security criteria. Moreover, WPS paperwork makes it possible for welders to replicate successful welding treatments, leading to constant outcomes throughout different jobs.
In significance, the thorough development and stringent adherence to Welding Treatment Specifications are paramount for upholding the honesty of bonded structures, protecting versus possible hazards, and supporting the track record of manufacture firms for delivering top quality products and solutions.
Trick Components of Welding WPS
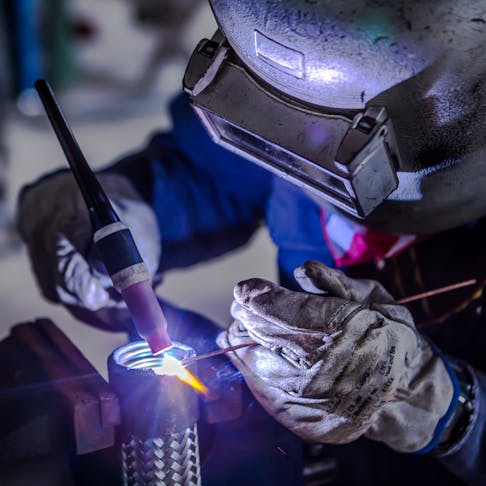
Enhancing Efficiency With WPS
When optimizing welding operations, leveraging the crucial aspects laid out in Welding Treatment Requirements (WPS) comes to be essential for improving processes and taking full advantage of efficiency. One way to enhance effectiveness with WPS is by thoroughly choosing the suitable welding specifications. By adhering to the particular guidelines provided in the WPS, welders can ensure that the welding equipment is established appropriately, bring about high-grade and regular welds. Furthermore, complying with the pre-approved welding sequences detailed in the WPS can significantly lower the moment invested on each weld, eventually increasing overall performance.
Frequently assessing and updating the WPS to integrate any kind of lessons learned or technological improvements can additionally contribute to effectiveness improvements in welding procedures. By embracing the guidelines set forth in the WPS and constantly looking for means to optimize processes, producers can attain greater efficiency levels and remarkable end outcomes.
Ensuring Safety And Security in Fabrication
Guaranteeing safety in manufacture involves a complex method that incorporates various aspects of the welding process. Welders have to be furnished with suitable equipment such as helmets, handwear covers, and protective clothing to minimize dangers associated with welding tasks.
Moreover, adherence to appropriate ventilation and fume extraction systems is crucial in preserving a healthy and balanced work setting. Welding fumes include unsafe substances that, if breathed in, can pose severe health dangers. Applying effective air flow actions helps to minimize direct exposure look at this now to these hazardous fumes, promoting respiratory system health among employees.
Normal equipment upkeep and examinations are also necessary for ensuring security in construction. Damaged machinery can result in crashes and injuries, underscoring the significance of regular checks and prompt repairs. By focusing on precaution and fostering a culture of understanding, manufacture centers can create a efficient and safe workplace for their employees.
Implementing WPS Best Practices
To enhance functional efficiency and make certain quality end results in fabrication procedures, incorporating Welding Treatment Specification (WPS) finest techniques is critical. Picking the suitable welding procedure, filler material, and preheat temperature defined in the WPS is essential for attaining the other desired weld high quality. Ensuring that qualified welders with the essential certifications bring out the welding treatments according to the WPS guidelines is vital for uniformity and reliability.
Final Thought
To conclude, welding WPS plays an essential function in making certain efficiency and security in manufacture processes. By concentrating on crucial elements, boosting efficiency, and executing finest techniques, firms can optimize their welding operations. It is necessary to focus on safety and security measures to stop mishaps and make certain a smooth manufacturing procedure. By adhering to these methods, organizations can unlock the complete possibility of welding WPS in their fabrication operations.
In the world of manufacture, Welding Treatment Specs (WPS) stand as the backbone of welding operations, dictating the necessary steps for accomplishing both effectiveness and safety and security in the manufacture process. By specifying crucial criteria such as welding procedures, materials, joint styles, preheat temperatures, interpass temperatures, filler steels, and post-weld warm treatment requirements, WPS provide a standardized strategy to welding that boosts effectiveness, high quality, and safety in manufacture procedures.
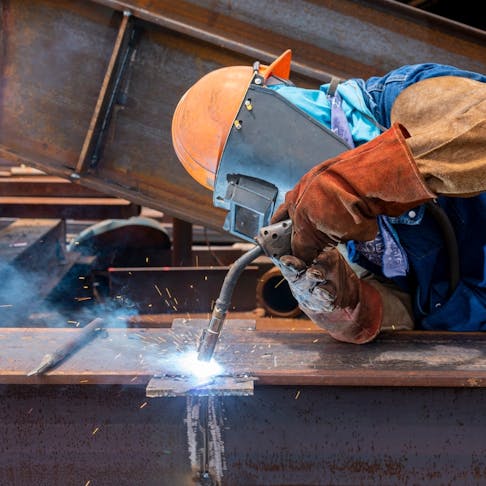
When optimizing check my reference welding operations, leveraging the vital elements detailed in Welding Treatment Specifications (WPS) ends up being essential for improving procedures and maximizing efficiency. (welding WPS)
Comments on “Optimizing Your Welding WPS: Techniques for Improved Efficiency and Performance”